Dawn of the digital manufacturing world
Customized products require batch-sizes of just 1
New assembly line for scrubber driers
Manufacturing up to 40,000 variants of one and the same product in an economical way – this is the challenge Kärcher must confront when manufacturing scrubber driers. This will only become possible using a new manufacturing concept which employs Industry 4.0 principles. The modern assembly line was designed by Kärcher's production facilities department in collaboration with the Fraunhofer Institute for Labour Economics and Organisation (IAO) in Stuttgart and simultaneously built into a working production process within just two months. For over a year, the production line has been operating with great success. Plant manager Carsten Schlenker explains: "The increasing number of product variants makes batch-optimised manufacturing evermore difficult. New equipment details further increase the complexity. Thanks to the new production line, single-piece production is now possible in an economically viable way, and even building new variants is a simple process."
The starting point for each individual manufacturing contract is the machine as configured by the customer themself. They are able to choose between many variants with a wide variety of equipment features, adapting the machines to the relevant requirements and local conditions. There are, for example, four different suction motors available, allowing the machine to be adapted to suit voltage and frequency of the local power supply, or equip it for battery operation. The scrubber head is also offered in a number of variants – as roller or disc variants, each in several different widths and diameters. The control panel is currently manufactured in 13 variants – multiplying this variety alone results in countless end products.
New technologies set to start:
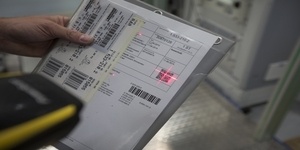
Scanning the QR code
Each assembly order is assigned a QR code. When the code is scanned, the order data with all of the details relating to the ordered machine are transferred to a rewritable RFID tag and a parts list with all of the single parts required for assembly, right down to the tiniest screws, is recorded.
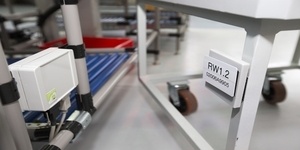
RFID tag on assembly cart
The RFID tag is attached to a specific spot on an assembly cart.
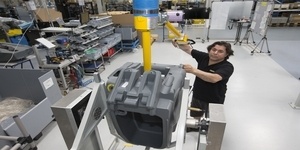
Tank module already installed
In this specially designed mobile frame, the machine's large fresh and dirty water tank, which consists of just one part, is already installed.
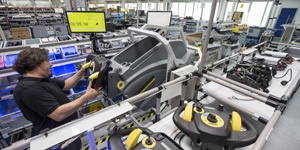
Assembly of additional components
The employee now moves the cart along the assembly line and fits the next components such as hoses, valves, filters and control panel onto the tank in a defined sequence. This involves the cart passing through several stations, in which the components and fastening material are in boxes ready to use.
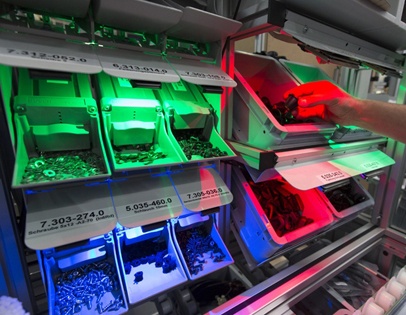
Pick-by-light system makes assembly easier
In keeping with Industry 4.0 solutions, the RFID tag on the assembly cart communicates directly with the production line's shelving system and activates the pick-by-light system. At each station, a green light indicates which parts are required for the machine variant currently being produced, and which boxes these parts can be found in. Monitors at each workstation also show assembly instructions.
A sensor above each box registers when a part has been taken from it and switches off the green light. The light above the box containing the next component simultaneously switches from blue to green. And if the employee reaches into the adjacent box by mistake, this is indicated by a red light.
Intelligent control of the testing station
Ultimately, the new system also enables intelligent controlling of the testing station. The machine configuration contained in the RFID tag is called up and an appropriate testing plan created. In this way, a scrubber drier is created which matches the customer's wishes, from ordering all the way to final testing.
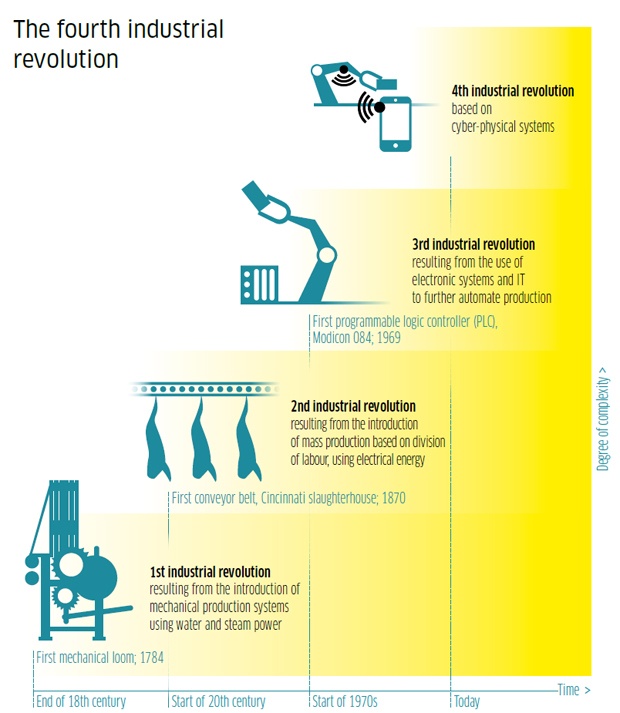
Deep cleaning of hard and resilient floor coverings with scrubber driers
Scrubber driers are used to clean floors with coverings such as PVC, linoleum, parquet, tiles or granite. Two work steps are mechanised with their help: scrubbing (wet wiping) and, immediately after this, drying the floor. This mechanisation allows both work steps to be carried out more effectively, more quickly and more economically than if carried out manually.
The machine combines two tools:
- one for scrubbing (roller or disc brushes)
- one for drying the floor
For scrubbing, fresh water and cleaning agent are mixed (individually dosed) - the cleaning solution as it is called - and directed onto the floor via the roller or disc. Due to the weight of the machine, the contact pressure of the brush is very high compared to manual wiping. This makes cleaning very effective and allows even stubborn, sticky dirt to be removed.
After scrubbing, the squeegees at the back of the machine collect the dirty water, the mixture of water, cleaning agent and dirt, and direct this into the tank which is intended for this purpose. The floor is dry immediately and can be walked on without the risk of slipping.

