Professional cement screed cleaning
Cement screed is the most commonly used type of screed. This floor covering requires special attention when it comes to cleaning and care. This is because it not only has to withstand a considerable amount of strain, but it also needs to meet occupational safety standards at the same time. For deep, maintenance and intermediate cleaning, it therefore all comes down to selecting the right equipment.
Special properties of cement screed
Cement screed is the most commonly used type of screed and consists of sand or gravel plus cement and water. The only type of screed produced in the industrial sector is "hard-aggregate floor screed", which can withstand extremely high traffic due to its thickness and strength class.
What makes cement screed unique is that when it is exposed to acids, it is given a structure similar to that of exposed aggregate concrete, i.e. the concrete becomes rougher and harder to clean. In the case of high gloss floor coverings, cleaning with strong alkalis (pH value of higher than 10) can also result in a matt surface finish.
In addition, in the absence of surface treatment measures, – such as impregnation, sealing or coating – cement screed tends to lead to dust formation. In addition, dirt and moisture can penetrate more quickly. If the cement screed is not treated, care should be taken during cleaning to ensure that the moisture applied is sucked back up again. In this instance, cleaning should only be carried out using the one-step method.
Cleaning preparation (initial cleaning/final cleaning on building sites)
Prior to wet cleaning, very large dirt can be sucked up using a vacuum sweeper, as required and depending on the type and amount. Stubborn dirt left after the construction phase, e.g. varnishes and paints, mortar, dispersion paint, tar and adhesives, is carefully removed using a spatula or blade.
Remove residues of...
- mortar using a green hand pad.
- dispersion paint by applying undiluted deep cleaner for approximately five minutes and carefully working it using a green hand pad. Then rinse the area thoroughly afterwards. Please note: Not for use on self-gloss emulsions or polymer coatings.
- Carefully work the varnish/paint/adhesives using a universal stain remover. Add the solvent to a cloth and work the paint, varnish or adhesive residues using a soaked cloth. However, never use a dilution on self-gloss emulsions, e.g. a polymer dispersion, because it will damage the coating.
Maintenance cleaning: Removing light soiling
Maintenance cleaning is carried out using the one-step method. To remove light soiling, the scrubber drier is fitted with red scrubbing brushes or pads. The scrubber drier works with a reduced contact pressure and lower roller brush speed. A suitable cleaning agent would be a maintenance and intermediate cleaner for industrial use diluted to between 0.5 and 3 per cent, depending on the amount and type of dirt. We also recommend equipping the machine with the automatic cleaning agent dosing function. Postwiping or rinsing is not required – the floor can be walked on again immediately.
If the cleaning job does not require wet cleaning, maintenance cleaning can also be carried out using a vacuum sweeper.
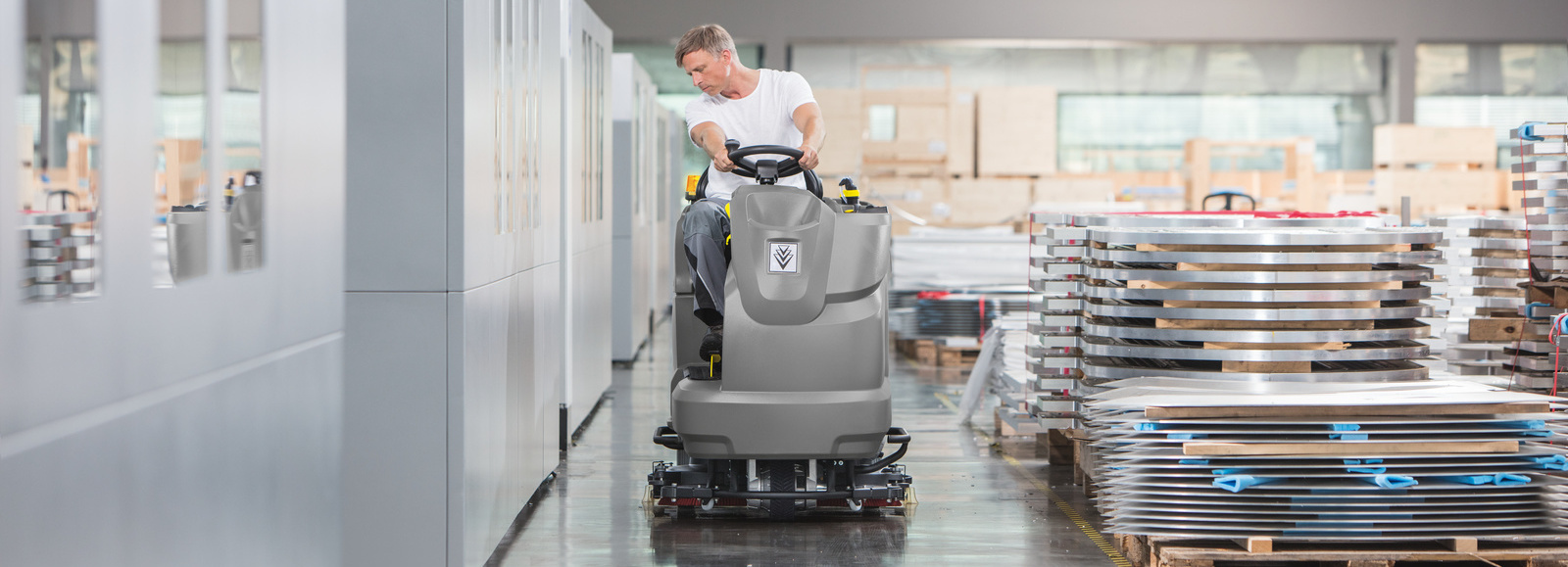
Deep cleaning: Removing very stubborn dirt
Dirt – such as oil, grease and tyre wear – which cannot be removed during maintenance cleaning is eliminated by performing deep cleaning at regular intervals. This requires powerful scrubber driers with a roller scrubbing head. If the floor covering allows, cleaning is carried out using a two-step method at full contact pressure with green scrubbing brushes or pads. The procedure should always be performed step by step to avoid the floor getting too wet or the cleaning solution drying out again quickly.
If protective films need to be removed in addition to oil and grease, we recommend using an all-round deep cleaner or an intensive deep cleaner as the cleaning agent. The cleaning agent is diluted to 50 per cent for removing protective films.
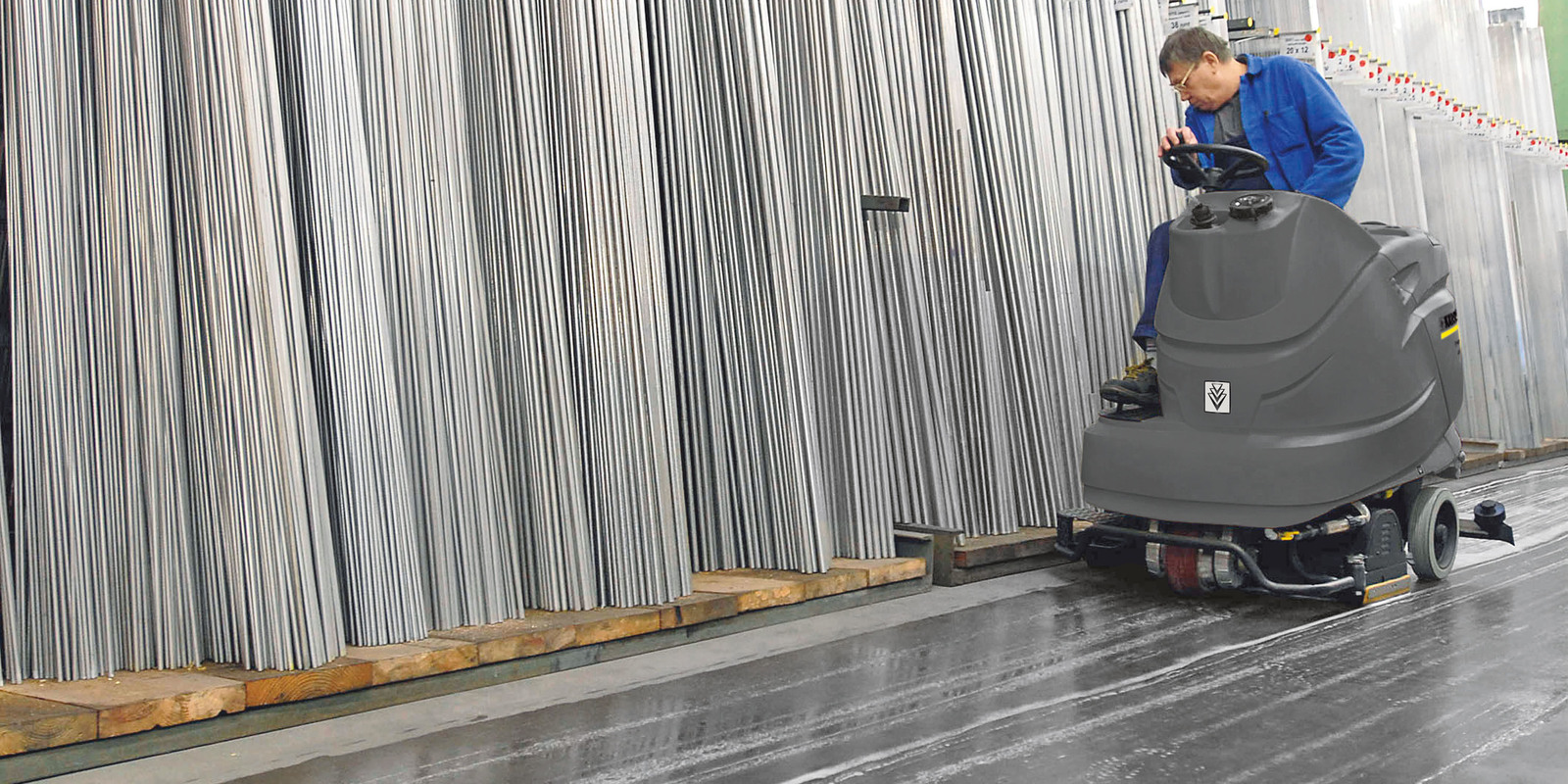
Step 1: Use a scrubber drier to cover the area that needs cleaning with cleaning agent and then scrub it two or three times until all the dirt has come loose.
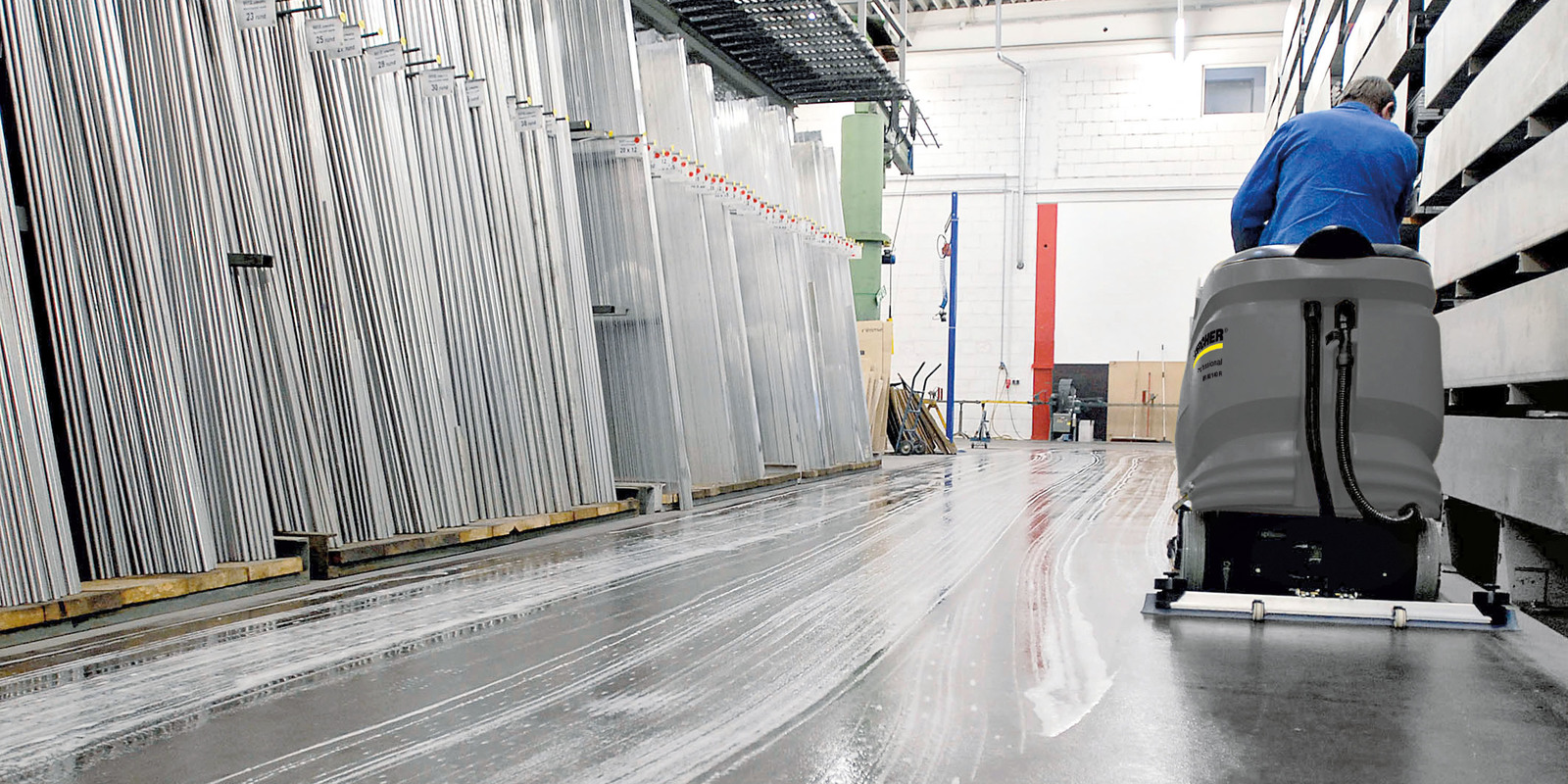
Step 2: Remove the dirty water using the squeegee and the vacuum function on the machine. Then cover the entire area with clean water again and proceed using the one-step method: Cover with water – scrub – use suction.
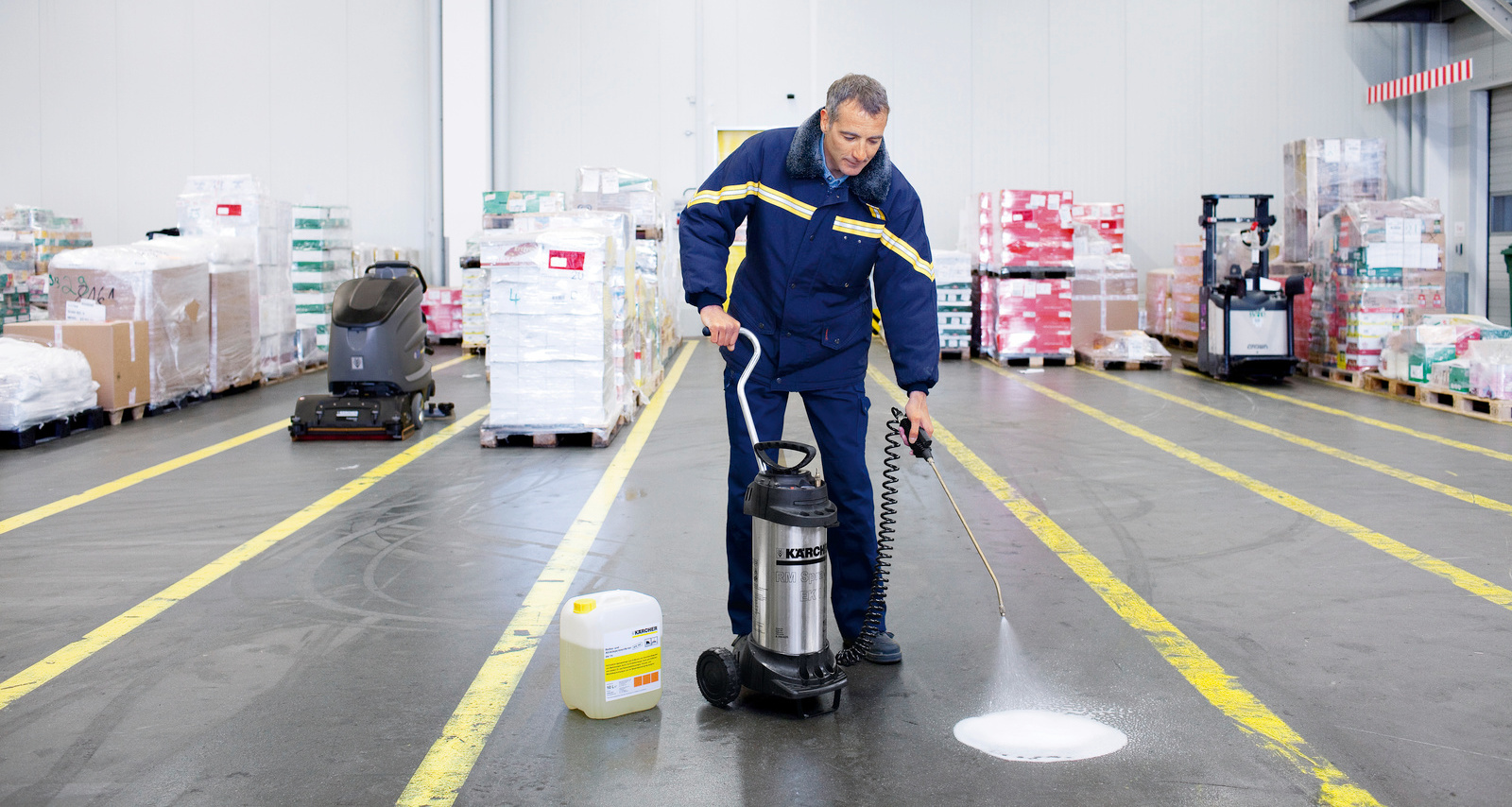
Removing skid marks and tyre tracks
To remove the skid marks left by forklift trucks or abrasions from tyres, use a cleaning agent that is NTA-free and has been specifically developed for this purpose. Apply it undiluted to the dirty areas using a cleaning agent sprayer or spray bottle and leave it to work for a few minutes. Then work the area using a scrubber drier without adding cleaning solution. The roller scrubbing head should be fitted with green roller pads or roller brushes depending on the structure of the surface (smooth or textured respectively). The next step is to remove the dirty water and then rinse with clean water (one-step method).
Please note: Do not use this method on polymer-based or wax coatings, as the cleaning agent may remove them.
The right choice: Scrubber driers with roller scrubbing head
For stubborn dirt and heavy soiling, we recommend using a scrubber drier with a roller scrubbing head for wet cleaning. Smooth surfaces are cleaned using roller pads, while rough and textured surfaces are scrubbed using roller brushes. The high cleaning efficiency is down to the following:
- Brushes/pads running in opposite directions
- High and uniform contact pressure (up to 260 g/cm2) across the entire working width
- Extremely high speed (max. 1100 rpm)
- Excellent floor contact
These properties make it possible to remove the dirt safely from the floor. The high speed also generates a self-cleaning effect, meaning that the cleaning efficiency remains consistently high. Sweeping the floor in advance is often unnecessary for light, loose dirt as the roller brushes move in opposite directions to sweep the coarse dirt into the integrated sweeper drawer.
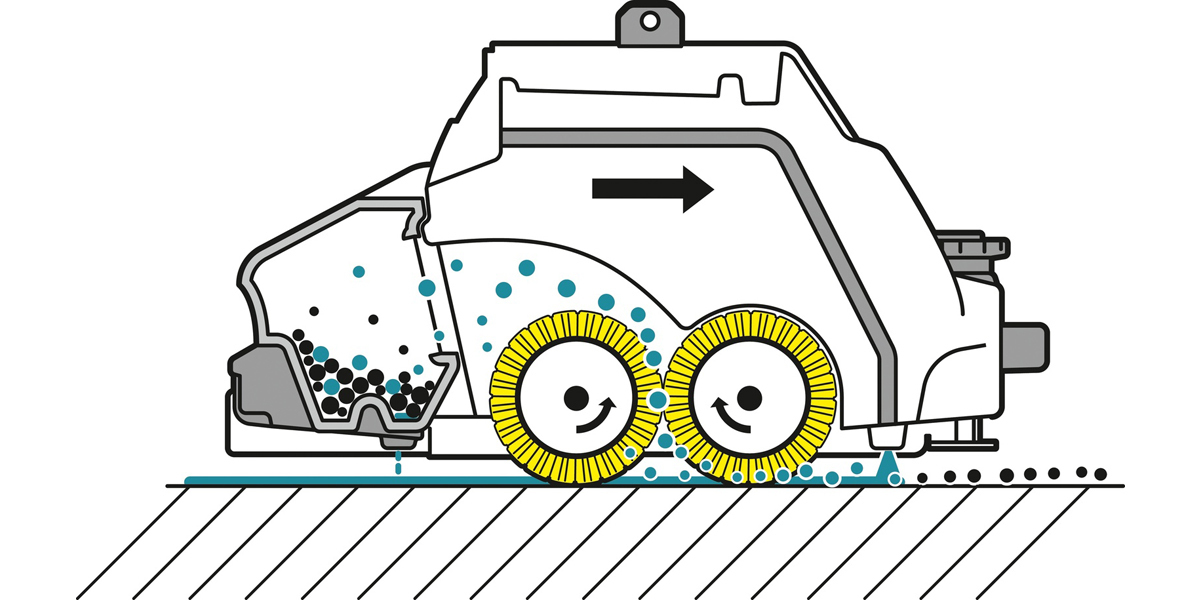
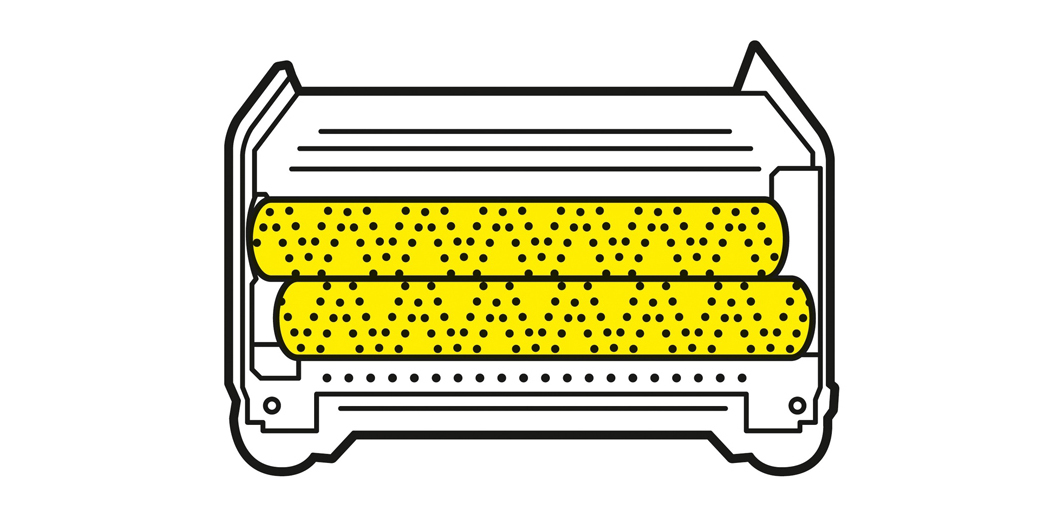