Everything is connected
Digitalisation, artificial intelligence and robotics: technology mega trends are driving huge disruption to the world of manufacturing across the planet. Humans, machines and processes are becoming ever more closely interwoven as we strive to improve productivity. In many cases, physically strenuous work is being eliminated for employees and replaced by other tasks requiring expertise in this evermore - complex production environment. Nobody knows exactly where we are heading – but the journey is certainly an exciting one!
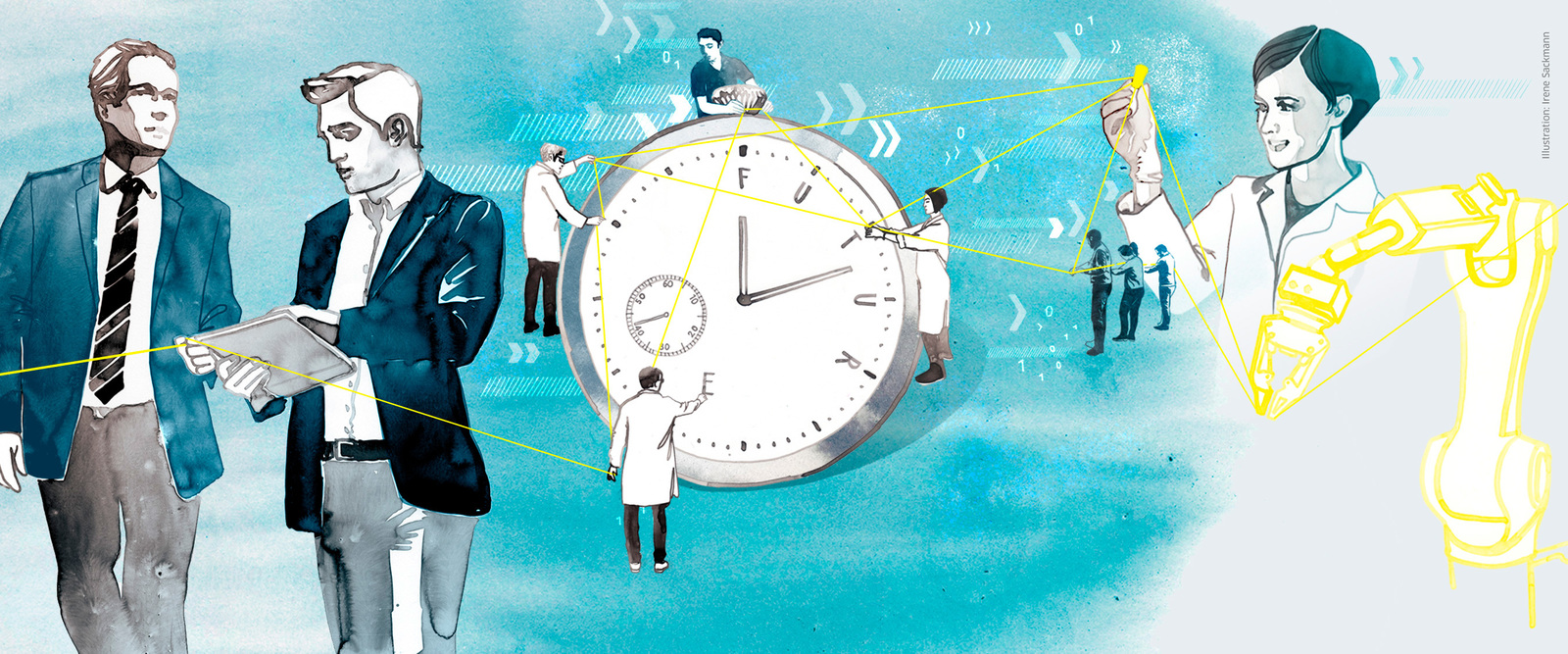
A tangible future
For example, in Bühlertal
Manufacturing locally while remaining competitive. Implementing client requests in high quality at high speed. Assuring the longterm existence and sustainability of our site. Kärcher is heading in this direction and going fully digital at the Bühlertal site. Even before the Bühlertal 5.0 project started, the plant was already over 50 % automated. Within just two years, production control, manufacturing and intralogistics had all been introduced or further automated. But why do driverless vehicles need swarm intelligence and why do employees now have to carry much less weight? Let’s take a look.
Taking seasonal work digital: business goes on
Large projects have a habit of petering out before they come to anything. This is a particular problem when the scope is too big and employees are not on board. Katja Räntzsch, project manager for Bühlertal 5.0, explains: “Right from the start, it was important that all staff were involved because they are the ones who will have to take on many of the tasks in the implementation process. That can only happen if they are motivated and open to new ideas – not to mention that business goes on and we have to reliably run the operational side of things, too.”
In Bühlertal, operations comprise, for example, in-house plastic manufacturing of 50,000 components every day and the production of 25,000 products for domestic and professional use. Then there is the particular challenge posed by cleaning technology being a seasonal business. In the retail segment, demand for high-pressure cleaners is especially high in spring and summer. “As soon as the sun comes out, orders spike and they need fulfilling quickly – so we work with a team of 570 permanent staff plus an additional 300 seasonal staff across three shifts,” explains Räntzsch.
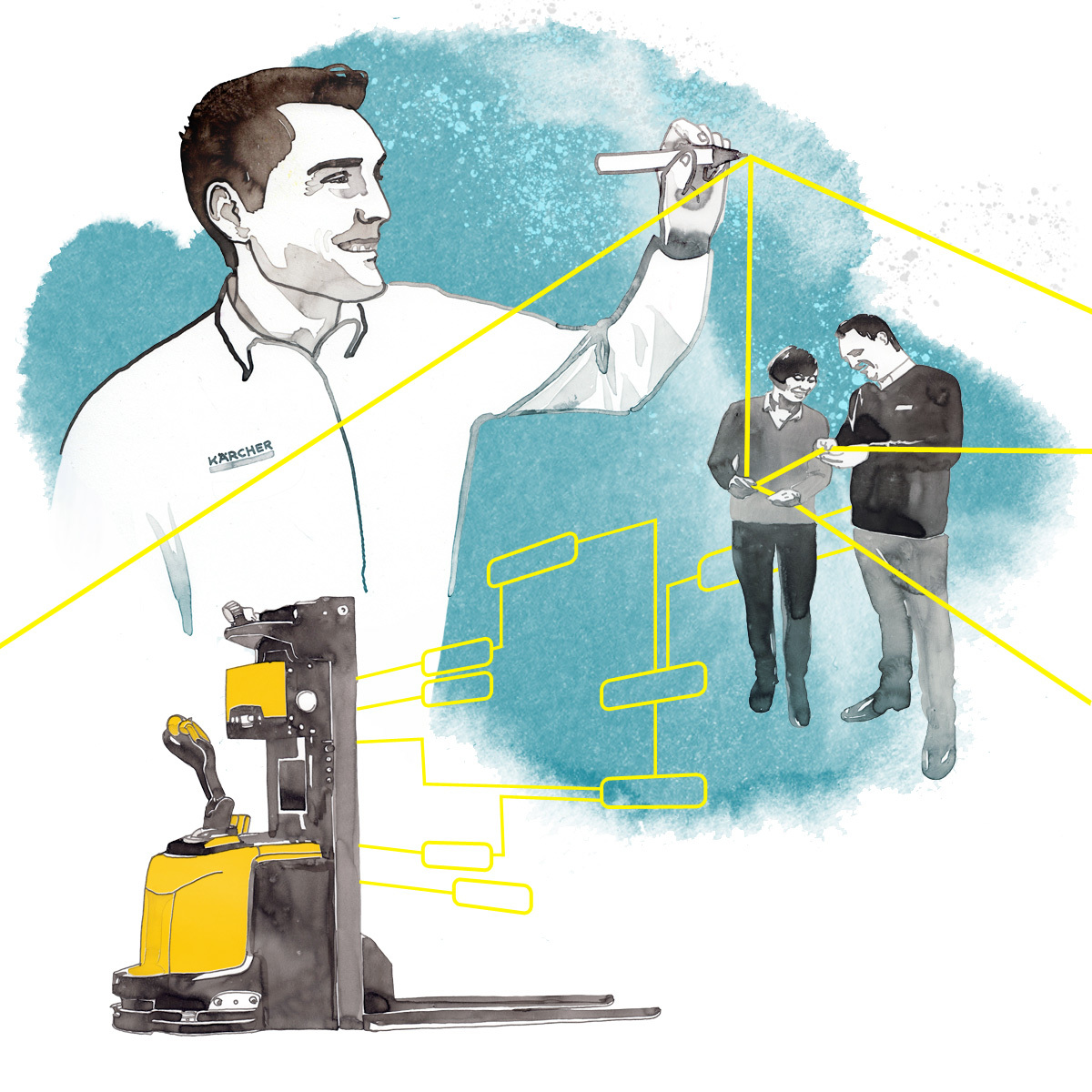
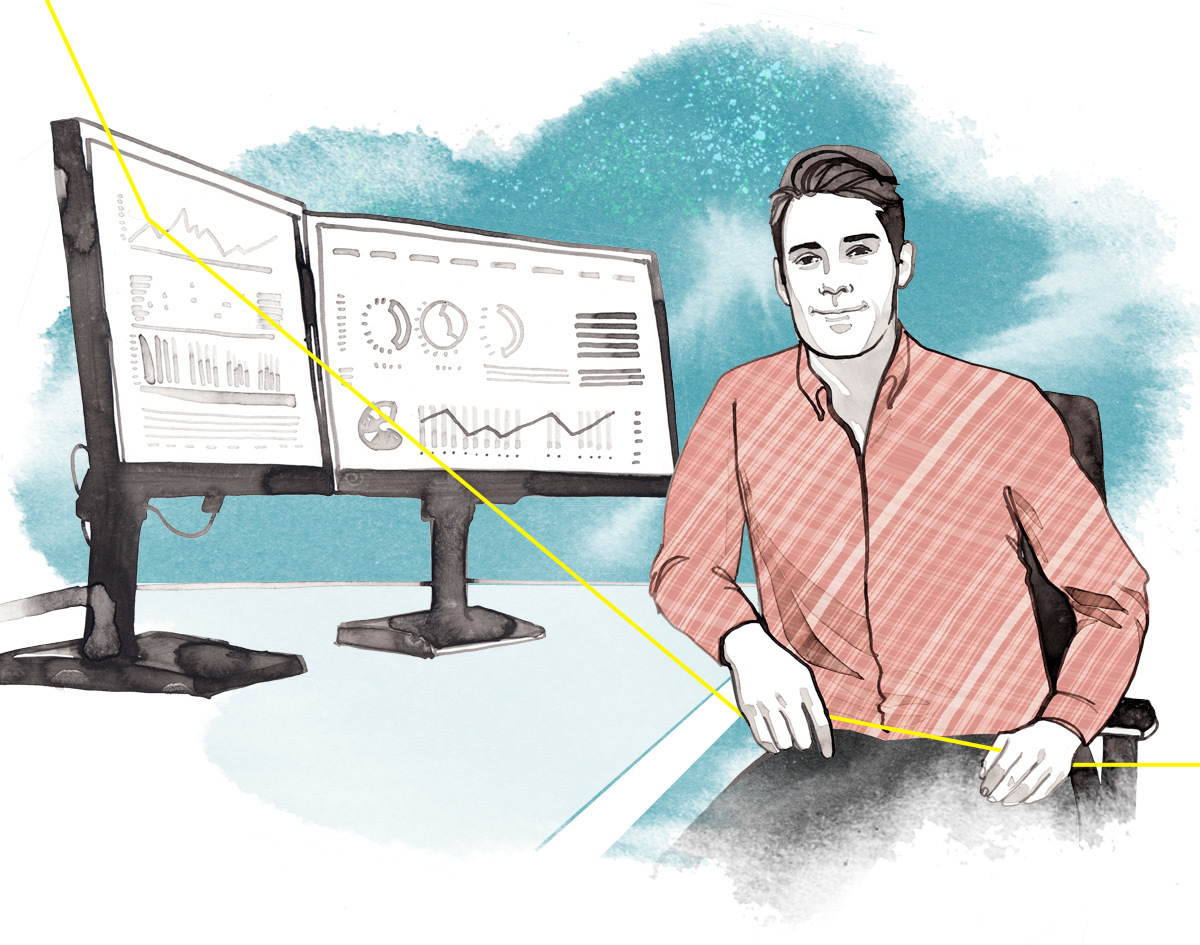
No pipe dreams, please. We choose topics and tackle them.
Once a project to tackle has been identified, a suitable digitalisation strategy must be selected. “We are not interested in commissioning large, tailored programming projects which then simply do not work,” says Räntzsch. “We use fairly standard solutions which already work and simplify processes using software where we can.” The foundation for all of this is high-performance, failure-resistant Wi-Fi and the right in-house network – so expanding our digital infrastructure was the first pillar of the project. Then we turned to the core issues of production control, automation and intralogistics. An MES system is at the heart of our production software, and it will be expanded incrementally with SAP interfaces by 2021. “We used to use Excel a lot, as manysites do,” acknowledges Räntzsch. “That works, but it is labour-intensive and relies on just a few experts.” The new system is even able to handle all of the detailed production planning, from preproduction to final assembly and all the way to quality control. “At the moment, we are finding potential for optimisation on an almost daily basis,” says Räntzsch. “For example, our injection moulding machines have always had high capacity utilisation, but the MES has managed to improve this.”
Humans and machines: working hand in hand
The digital revolution has hit the world of work, and some companies are automating with the goal of reducing staffing levels. Katja Räntzsch explains why that is not the goal in Bühlertal: “At the core of all of this is the goal of increasing the plant’s output – by improving working conditions and smoothing processes." So the production lines were analysed, showing where work could be made easier. The final assembly of the K2 pressure washer involves manually installing the 2 kg pump – a very strenuous and not particularly ergonomic task when repeated over and over. From 2020, this task will be completed by a machine. Steps will also be taken to ease the strain of working on our professional products. This will be particularly advantageous when dealing with the heavy machines. “Just like in the automotive industry, underride driverless transport systems will take the HDS high-pressure cleaner to each workstation in future – greatly improving ergonomic standards.” Once a product is ready to be picked up, the packaging robot places it on a pallet. The machines are then picked up by a driverless transport system (DTS). “This is truly fascinating technology,” reports Räntzsch. “And the DTSs work using swarm intelligence. They don’t simply complete a route; the DTS closest to the current task will pick the product up.” Then it goes to the warehouse or to direct dispatch – where the plant has improved its quota from 30 % to 50 % using the measures already implemented, with a goal of 70 % going forward. “Direct dispatch means orders are addressed and sent out quickly, with minimal storage costs.”
Well on the way – but not there yet: progress is motivation
Many initiatives have been or are in the process of being implemented in Bühlertal – and that is all within two years. “We are well on the way to becoming a paperless factory, as well,” reports Räntzsch. In keeping with the digitalisation strategy for the whole company, we are setting up HR management at the plant so that employees who do not have their own computer can request holiday and report sick leave using digital terminal devices. Increased productivity and a reduction in costs caused by errors are the proof that all of this is working. “This project is not the end for us, though; it is just the beginning,” says Räntzsch with a smile. “Because we want to go a step further every day, just like we have been doing so far – there is always more that can be done.”
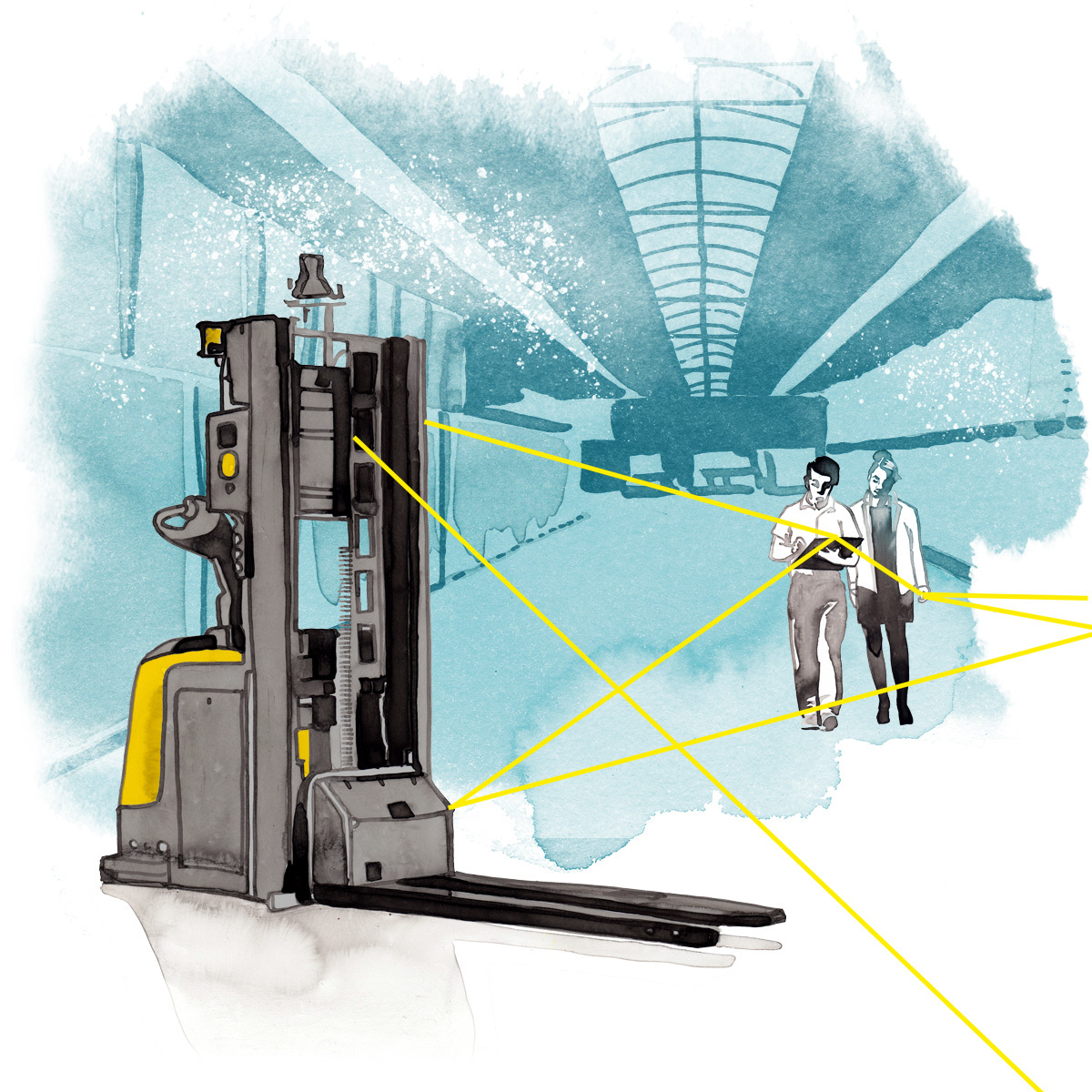
Facts and Figures Bühlertal 5.0
In demand at Jungheinrich: INTRALOGISTICS TO COMBAT WASTE *
Jungheinrich specialise in intralogistics solutions, and they provided support for Kärcher with the Bühlertal 5.0 project. What are the biggest challenges today?
Markus Staringer: For a start, we rarely implement our solutions on a blank slate. We usually work on the basis of existing processes and assembly workflows. We work with our customers to investigate where resources are being wasted on things like unnecessary journeys, waiting times and storage. Then we optimise processes using this as a basis. There is very high demand for system availability. To assure availability, we have around 8,000 customer service technicians on duty so that we can remedy any issue in the shortest possible time.
Processes are overlapping more and more – primarily bridging intralogistics and production. Where do you see the greatest potential for more efficiency?
Markus Staringer: That only becomes clear when you look at the process chains. At Kärcher, for example, the merchandise leaves the injection moulding machine, then the injection moulded parts go to production and finally the products go to the warehouse or to dispatch. If these steps run automatically, the risk of error is significantly reduced and work can continue uninterrupted, with reliable cycle times. All of that means that investments in intralogistics pay for themselves quickly.
Digitisation, automation and artificial intelligence – the magic three. Much is already possible, but what will the future hold?
Hennes Fischbach: There has been a constant trend towards automation in intralogistics for decades now. Current solutions are incredibly reliable and our customers really value that. You see, the mantra is: the production environment is far too sensitive for experiments. Artificial intelligence is a buzzword tied up with all kinds of visions and dreams these days. What AI really means is that machines are able to learn and, within a specific framework, independently find the right solution. It also means that we as humans are delegating more responsibility to machines. It will be some time before we are really ready for that and sure that it is safe.
*Markus Staringer and Hennes Fischbach are project managers at Jungheinrich and supervised the Bühlertal 5.0 project.
You may also be interested in:
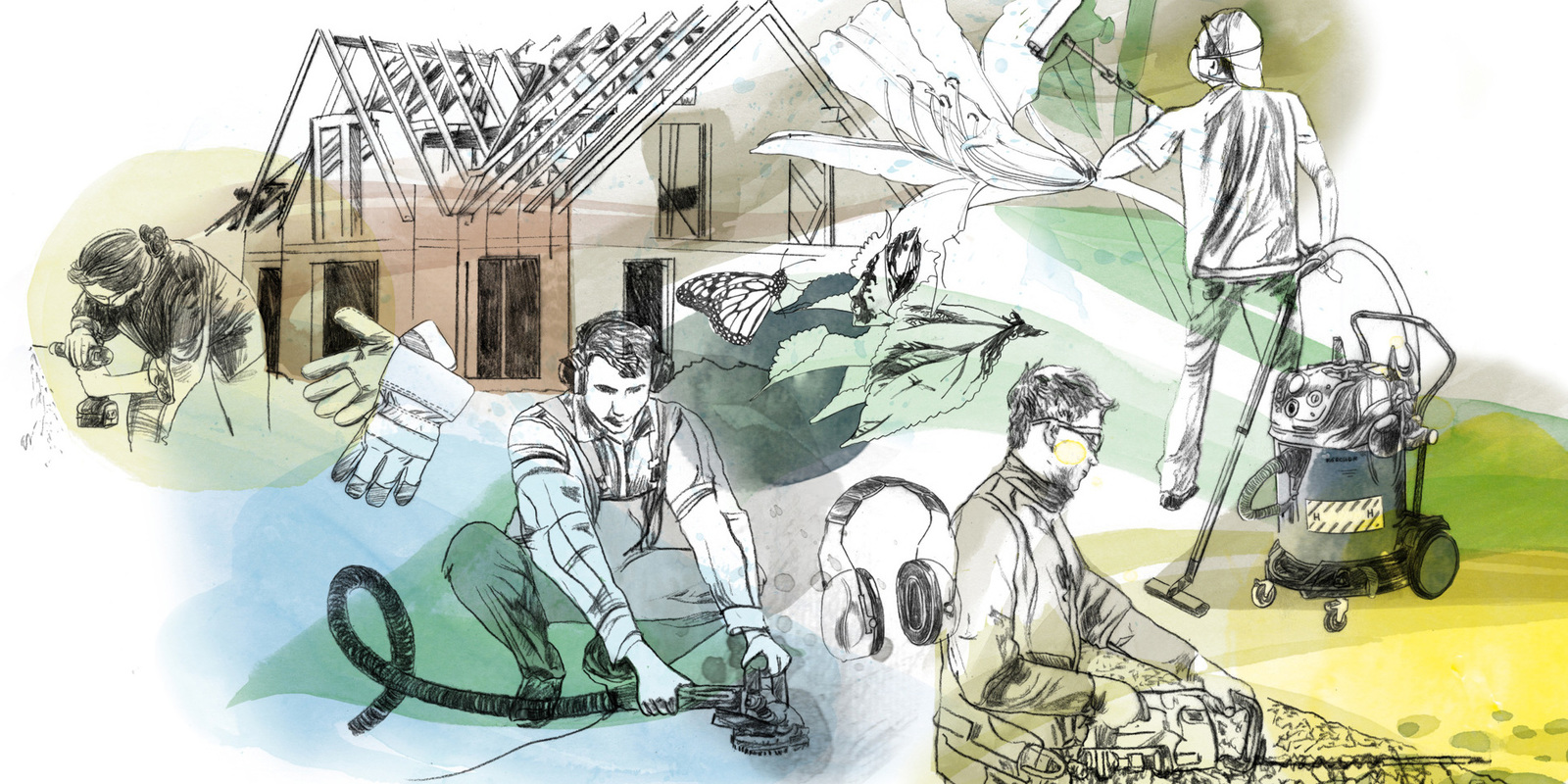
Two worlds, one goal: perfection
Kärcher at home on the patio. Kärcher in building cleaning. People most often think of these two areas of application when it comes to vacuum cleaners, high-pressure cleaners, etc. But it is hard to imagine everyday life without many Kärcher products, especially for workshops.
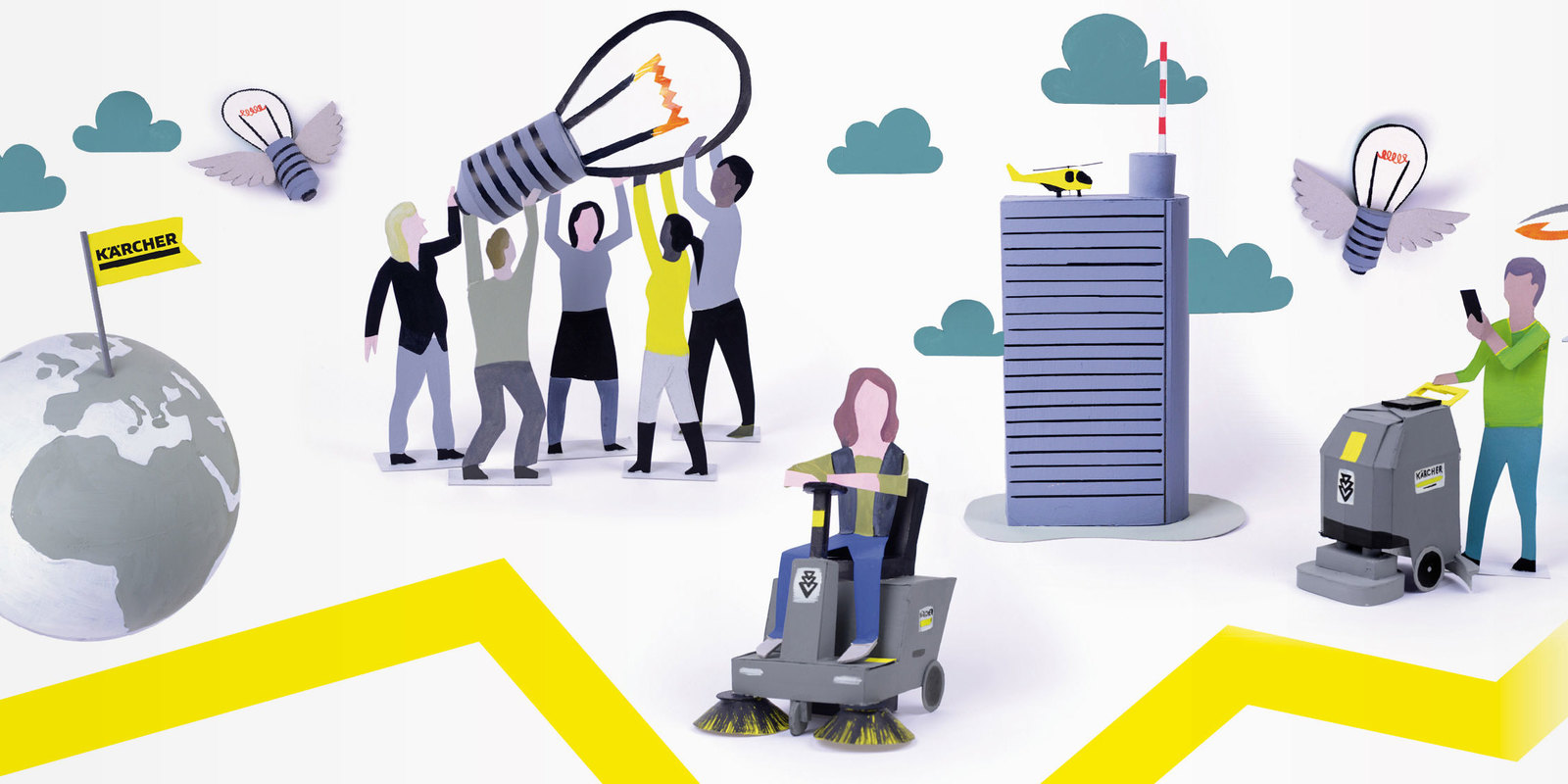
Let ideas take flight without losing touch
One company exists for several decades, has thousands of employees and is active all around the globe. Another company is brand new, so to speak, is made up of five believers and a great idea. It is a known fact that these two worlds can work very productively together and create innovations. It is also about bridging major differences.
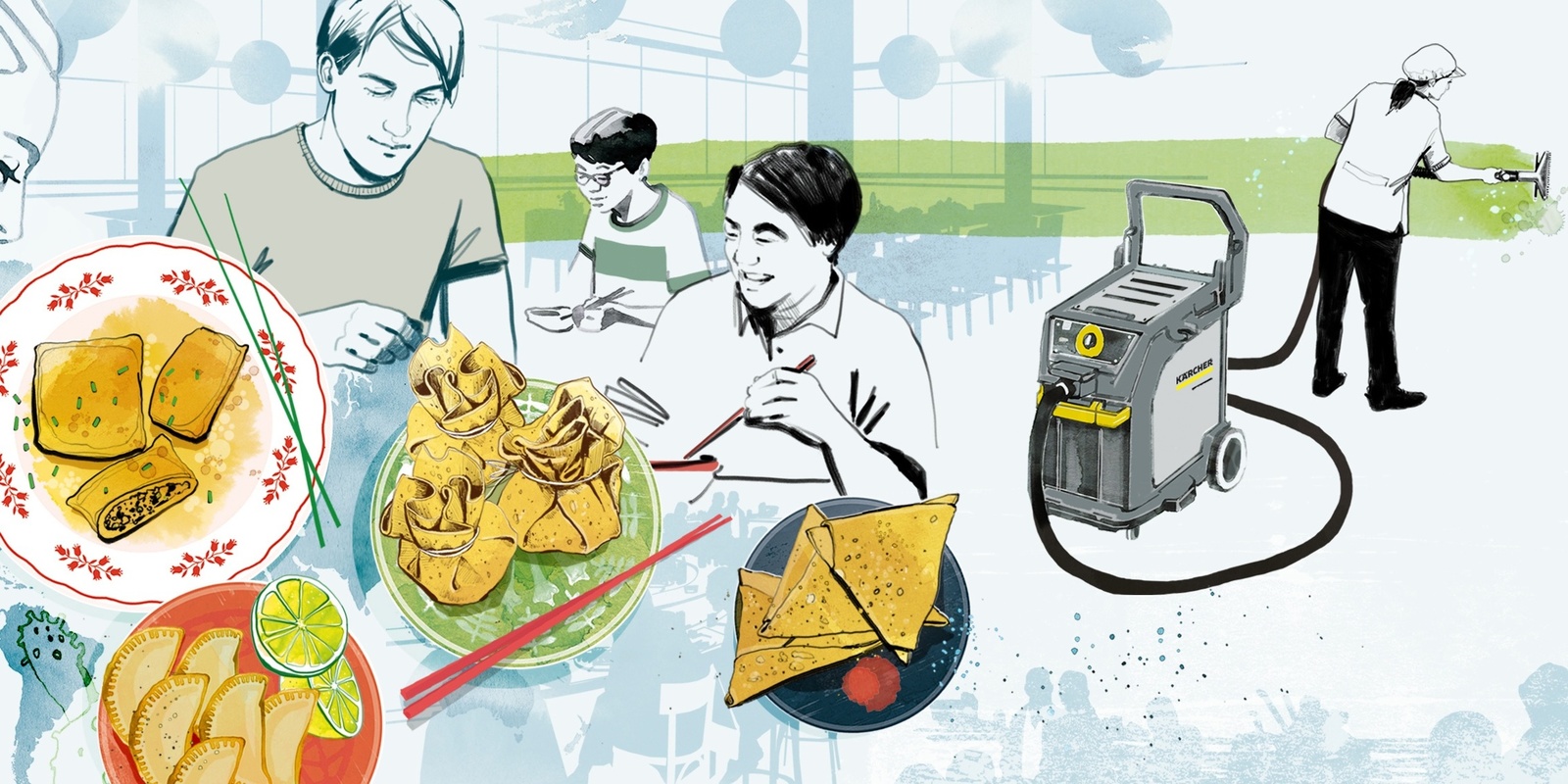
On the track of a swabian speciality
The Maultasche (Swabian ravioli) and Kärcher have one thing in common: they both hail from Swabia and can be found all over the world. Like Kärcher products, these delicacies wrapped in dough are popular around the globe. Join us for a brief journey that shows how culinary delights can bring people together and how cleaning technology can ensure carefree feasting.